When it comes to metal powders for additive manufacturing (AM), most conversations focus on the alloy itself, such as nickel, titanium, cobalt, stainless steel, and so on. But no matter how advanced the material is on paper, its real-world performance in the build chamber depends heavily on a less visible but equally critical factor: particle size distribution (PSD).
PSD is more than a technical data point buried in a material spec sheet. It’s one of the most influential variables determining whether a powder feeds consistently, build reliably, and produces fully dense, high-integrity parts. For manufacturers operating at the sharp end of aerospace, defense, energy, & medical production, small variations in particle size distribution can translate into major swings in process stability, part quality, & production cost.
At Continuum Powders, particle size distribution isn’t just a metric we report—it’s a property we engineer, monitor, and control at every stage of production. In this article, we’ll explore why PSD matters so much, what makes it so technically challenging to control, and how Continuum’s approach delivers powders that perform predictably, batch after batch.
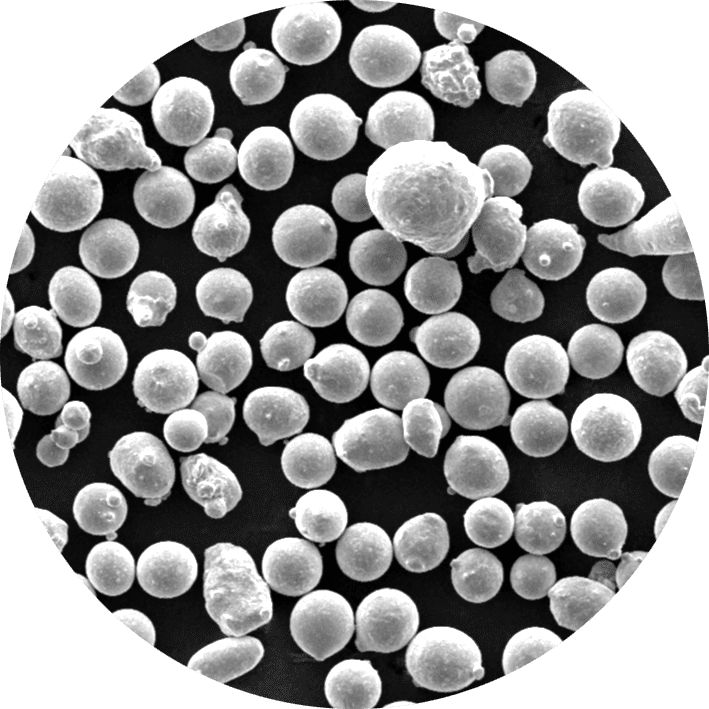
OptiPowder Ni 718 at 140X Magnification
What is Particle Size Distribution?
At its simplest, PSD describes the range and proportion of particle sizes present in a given batch of powder. Metal powders for AM are rarely monodisperse—meaning the particles are not all exactly the same size—but instead exhibit a distribution of sizes typically measured in microns (µm).
For example, a powder described as “15-45 µm” means that the vast majority of particles fall between 15 and 45 microns in diameter, though some statistical outliers may exist slightly outside this range. The exact shape of the distribution curve — how much powder clusters at the low or high end of the range — has a direct impact on how the powder behaves during printing.
Why PSD Matters for Additive Manufacturing
In laser powder bed fusion (LPBF), electron beam melting (EBM), and other AM processes, powder particles are spread in extremely thin layers—often just 20 to 100 microns thick. The powder must flow smoothly, spread uniformly, pack consistently, and melt predictably. Poorly controlled PSD can compromise any one of these steps.
If too many fine particles are present, the powder may clump due to Van der Waals forces or excessive surface area, leading to poor flow and uneven layer deposition. Excess fines can also increase oxidation risk due to higher surface reactivity. On the other hand, excessive coarse particles reduce packing density, resulting in voids or lack of fusion defects in printed parts.
A tightly controlled PSD ensures:
- Consistent flowability across recoating cycles
- Stable layer thickness and uniform spreading
- Efficient packing density to minimize porosity
- Predictable laser or electron beam interaction for consistent melt pools
- Repeatable mechanical properties in the finished part
In short, PSD directly governs both the repeatability of the AM process and the integrity of the finished part.
Why Controlling PSD Is Technically Challenging
Controlling PSD in metal powders isn’t as simple as sieving raw material into the correct size bins. The distribution is influenced from the very beginning of the atomization process itself. The melting temperature, gas type and pressure, atomization nozzle design, and cooling rates all directly affect how large or small the droplets form during atomization, which then solidify into powder particles.
Traditional atomization processes often produce a broad PSD, requiring extensive post-atomization classification to isolate the target fraction suitable for AM. While this works, it leads to high yield losses, increased cost, and a growing inventory of unusable off-size powder fractions.
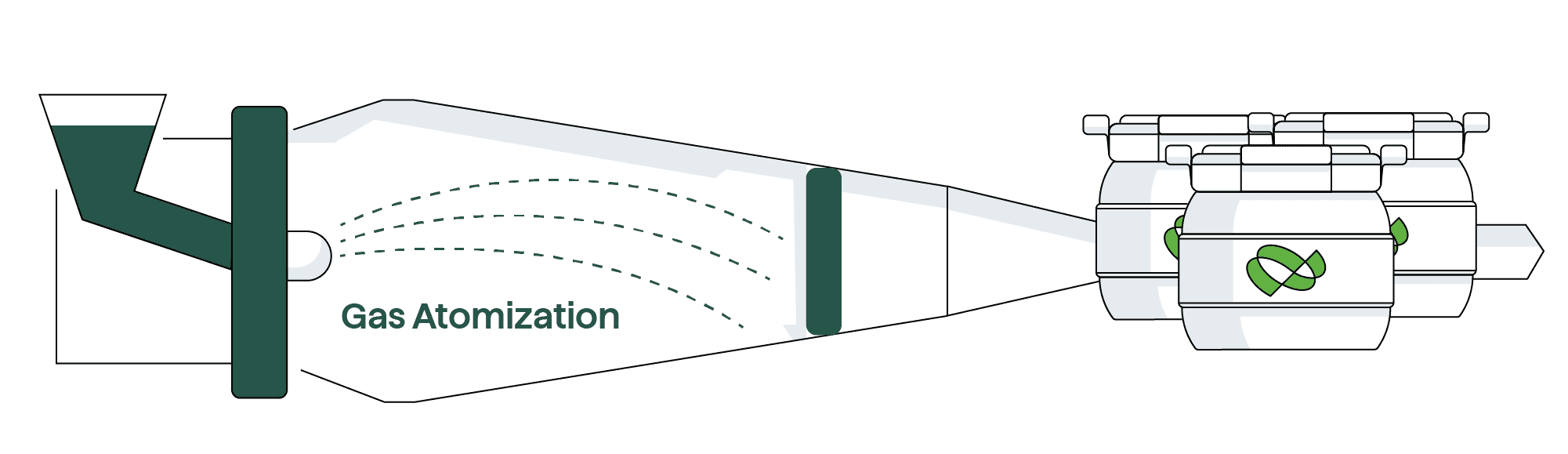
At Continuum Powders, our Greyhound Melt-to-Powder (M2P) gas atomization system allows us to engineer particle size distributions more precisely during the atomization process itself. By controlling atomization conditions, we produce narrower, more uniform PSDs that require less post-processing classification, increase usable yield, and deliver better powder consistency to our customers.
PSD Consistency Means Process Consistency
One of the persistent challenges in additive manufacturing is batch-to-batch variation in powder properties. Even small shifts in PSD between batches can force operators to recalibrate build parameters, increasing downtime, part variability, and scrap rates.
This is where Continuum’s OptiVantage quality framework plays a crucial role. Every batch of powder undergoes:
- In-line monitoring during atomization
- Particle size analysis using laser diffraction methods
- Lot-level documentation for full traceability
By producing powders with consistent PSD from batch to batch, Continuum allows AM users to focus on production—not troubleshooting.
The Sustainability Factor: High Yield, Low Waste
There’s an important sustainability dimension to PSD control as well. The more tightly PSD can be engineered at the point of atomization, the less powder needs to be discarded or reprocessed. In Continuum’s M2P process, high yields of usable powder mean more material goes directly into production, while less energy and resources are spent handling oversized or undersized fractions.
Combined with Continuum’s broader model of sourcing certified, high-integrity scrap as feedstock—rather than virgin-mined metals—our ability to tightly control PSD at scale directly supports both sustainability and cost-efficiency without compromising powder performance.
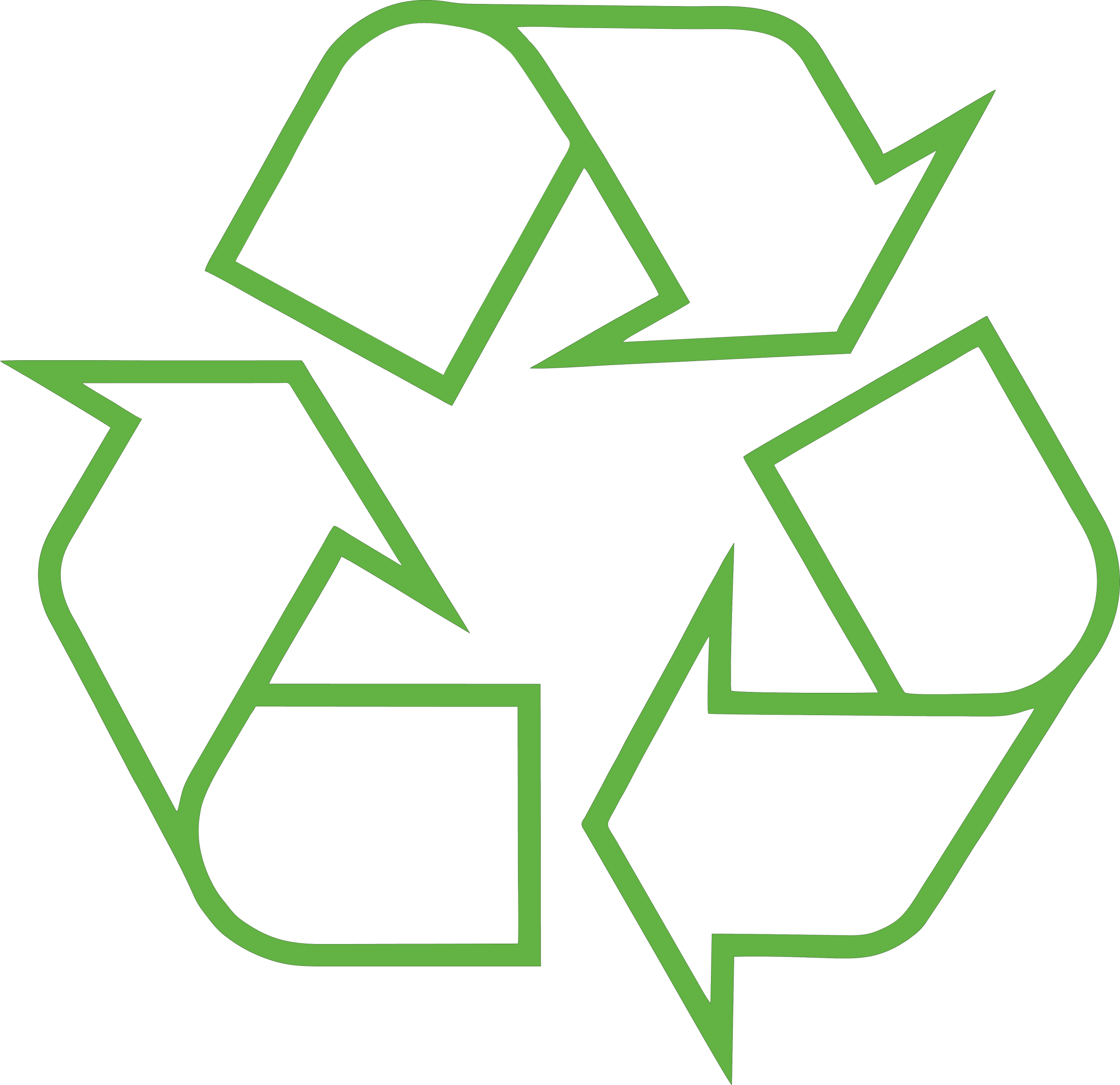
Why PSD Will Only Matter More in the Future
As additive manufacturing moves deeper into serial production of mission-critical parts, the industry’s tolerance for powder variability will only shrink. Applications in aerospace, energy, defense, and medical markets demand not only high mechanical performance but also statistical reliability across dozens or hundreds of builds.
PSD consistency is a foundational enabler of this industrialization. It reduces variability at the powder level, simplifies process qualification, and ultimately allows manufacturers to unlock the full scalability potential of AM.
At Continuum Powders, we believe PSD isn’t a byproduct of powder manufacturing—it’s a core product feature. It’s one of many technical levers we optimize to deliver powders that allow our customers to print reliably, scale confidently, and manufacture more sustainably.
The future of advanced manufacturing will be built layer by layer. Ensuring every layer starts with powder engineered for stability is how we’re helping make that future possible today.
Contact us today to learn more on how Continuum Powders can help you achieve your advanced manufacturing goals.