High-performance suppressors demand more than a clever design—they need materials that can take the heat, resist corrosion, and survive repeated firing. With additive manufacturing (AM), you can build suppressors with advanced geometries and better thermal performance, but the right metal powder remains the foundation.
Suppressors operate in a uniquely punishing environment. Choosing the right alloy means accounting for several high temperatures, thermal cycling, and corrosive conditions:
1. High-Temperature Strength & Heat Fatigue Resistance
Suppressors can exceed 600°C during sustained firing. Alloys like Inconel 718 (Ni718) and Ni7208 excel in these conditions, maintaining mechanical strength and resisting distortion, even under full-auto fire scenarios.
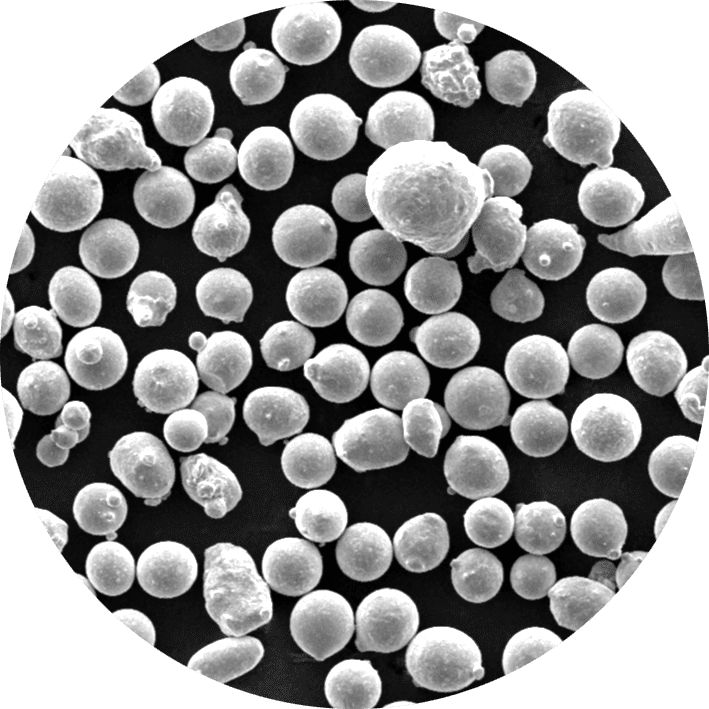
OptiPowder Ni718 – 140X
2. Corrosion & Erosion Resistance
Combustion gases introduce moisture, carbon residues, and other corrosive byproducts. Nickel-based superalloys such as Ni718 and titanium alloys are designed to resist this long-term chemical assault.
3. Fatigue & Crack Resistance
Suppressors face constant expansion and contraction during firing. Materials must offer exceptional resistance to thermal fatigue and crack propagation to ensure operational longevity.
4. Dimensional Stability & Build Integrity
Complex baffle structures and thin-walled designs require exceptional precision. That starts with powders that spread evenly, melt consistently, and avoid warping or porosity issues during printing.
Powder Characteristics That Make or Break AM Suppressors
Great alloy chemistry alone won’t cut it. The physical properties of the powder determine the success of each build:
- Spherical Morphology & Flowability
Smooth, round particles ensure uniform spreading during recoating. This prevents recoater drag, improves layer consistency, and minimizes defects in LPBF and binder jetting systems. - Tight Particle Size Distribution (PSD)
Suppressor parts demand tight PSDs—typically 15–45 µm for LPBF—to maintain dimensional accuracy and ensure clean surface finishes. - Purity & Low Interstitial Content
Even trace contaminants (oxygen, nitrogen, carbon) can reduce fatigue life and lead to cracking. In-house chemistry control is essential for mission-critical applications. - Traceability & Batch Consistency
Consistency matters. Each batch must deliver the same performance, with full traceability from source to powder to part.
Continuum Powders: Built for Suppressor Manufacturing
Continuum Powders was founded with one goal: deliver the highest quality metal powders for safety-critical, performance-intensive parts, including suppressors.
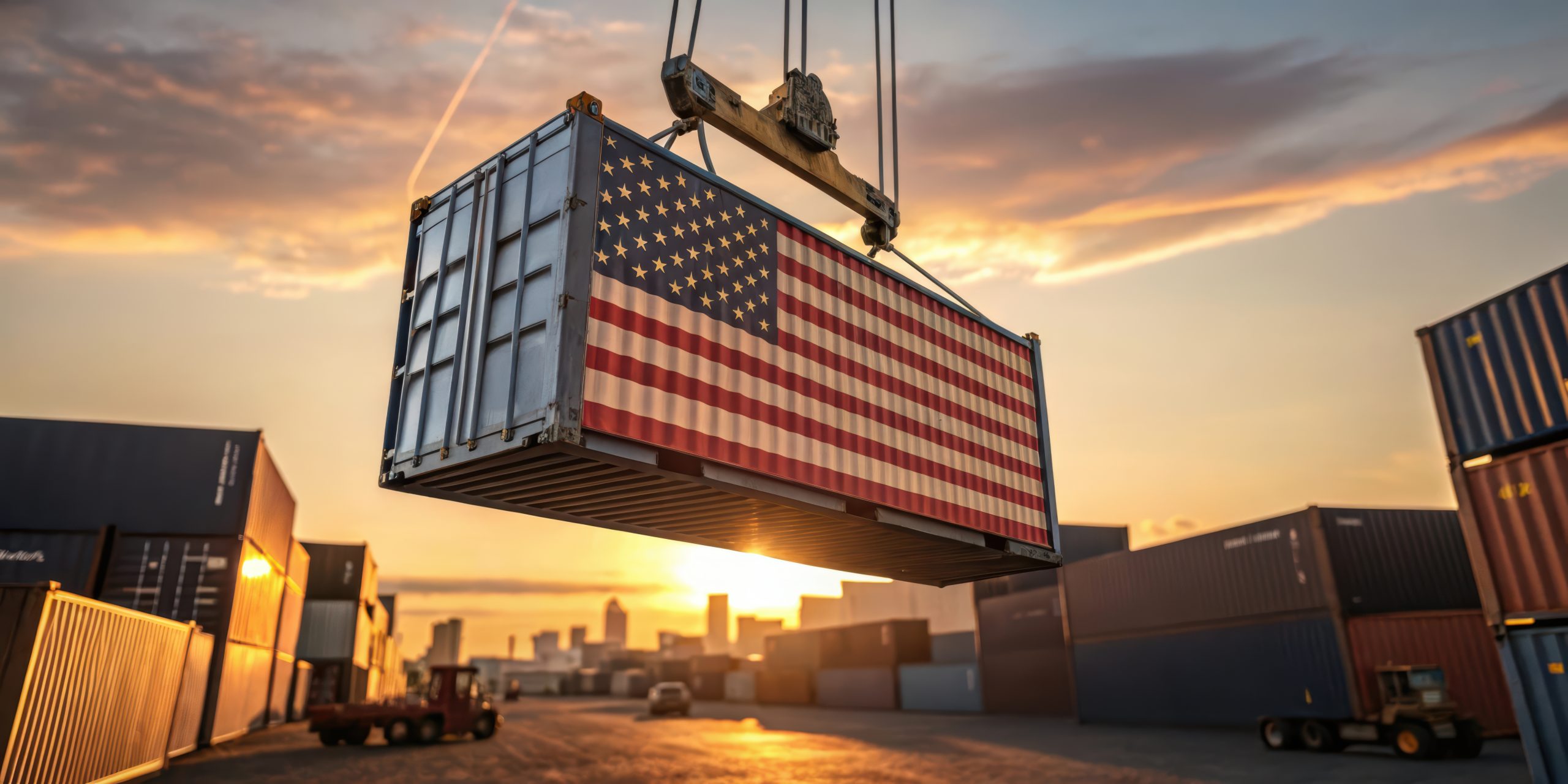
Proudly Designed, Sourced & Manufactured in the USA!
Our Process Advantages:
- Gas-Atomized Spherical Particles: Superior flowability and density for high-precision AM builds.
- Tight PSD Control: Application-specific ranges dialed in for suppressor geometries and system parameters.
- Certified High Purity: In-house analytical labs and scrap input validation reduce O/N/C levels across every batch.
- Sustainable U.S. Sourcing: We convert qualified domestic scrap into performance-grade powder, supporting sustainability goals without sacrificing material integrity.
- End-to-End Traceability: Full documentation and batch traceability for regulated and defense applications.
Common and Emerging Alloys in Suppressor Manufacturing
Design requirements dictate alloy choice, but high-cycle suppressors consistently rely on a few key materials:
Alloy | Key Benefits | Use Case Scenarios |
Ni718 | Outstanding strength at high temperatures, oxidation and fatigue resistance | Full suppressor bodies, high-heat and high-cycle environments |
Ti64 | High strength-to-weight ratio, corrosion resistant | Lightweight tactical and sporting suppressors |
Ni7208 | Exceptional heat suppression in fully automatic military-grade systems | Often selected for extreme thermal applications in defense |
Precision Starts with Powder
Suppressor designs are becoming more complex—and more capable. Additive manufacturing has opened new frontiers in geometry, weight reduction, and acoustic optimization. But none of that works without the right powder.
Continuum Powders partners with manufacturers to deliver AM powders that are consistent, build-proven, and application-ready. From advanced superalloys to high-strength titanium, we help ensure your suppressor performs under pressure—again and again.
Ready to take your suppressor manufacturing to the next level? Let’s talk.